Study on the Epoxy Resin Composites Prepared by Using Co Nanoparticle-Decorated Graphene Nanosheets as Thermal Fillers
Received Date: September 20, 2020 Accepted Date: October 12, 2020 Published Date: October 14, 2020
doi: 10.17303/jnsm.2020.6.102
Citation: Lifei Chen (2020) Study on the Epoxy Resin Composites Prepared by Using Co Nanoparticle-Decorated Graphene Nanosheets as Thermal Fillers. J Nanotech Smart Mater 3: 1-11.
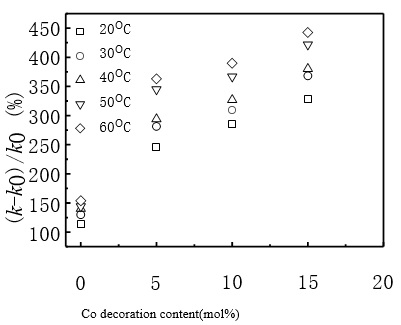
Abstract
The epoxy resin composites with high thermal conductivity have been prepared by using Co nanoparticle-decorated graphene nanosheets (Co-GNSs) as thermal fillers. Before being decorated by Co nanoparticles the GNSs are firstly modified using strong acid oxidation in order to improve GNS disperse in the epoxy resin. The Co nanoparticles decorating on the GNS surfaces can disperse well together with GNSs in the epoxy resin matrix. The Co nanoparticles linking the adjacent GNSs like a “bridge” and also act as “spacer” between GNSs to decrease the possibilities of GNS aggregation. The bigger size of the Co nanoparticles is good at the action of “bridge” and “spacer” and is desired to minimize the scattering of phonons because of the low interfacial thermal barrier. The Co-GNSs dispersing in the epoxy resin form not only 3D effective thermal conductive network but also an electrically percolating network. The generation of these 3D networks facilitates in reducing the Kapitza resistance and increases the transportation of phonons in the matrix. The synergistic effects between the Co nanoparticles and GNSs result in the obvious enhancement of the thermal properties of epoxy resin composites. When the decoration quantity of Co nanoparticles is 15mol% and the thermal filler content is 5wt% the thermal conductivity enhancement of the Co-GNS/epoxy composite reaches 327, exhibiting 2.86 times of that of the GNS/epoxy composite. By using this method to prepare epoxy resin composite, the lower filler loading make it possible to get epoxy composite with high thermal conductivity and perfect mechanical behavior.
Keywords:Epoxy resin composites; Thermal properties; Graphene nanosheets; Cobalt
Introduction
Epoxy is one of the most important polymers as the underfill material. It was widely used in microelectronic packaging due to its low cost, high mechanical properties, excellent dimensional stabilities, and easy forming process [1-5]. With the fast development of the electronics towards highly integrated, ultra-light, miniaturization, and multi-functionalization, the packaging density of the electronic components or the unit cells has dramatically increased [6]. Heat generation and accumulation will rapidly increase the operation temperature, and the high operation temperature will lead to the failure of components. The low thermal conductivity of pure polymer has become the main reason to limit their applications as microelectronic packaging materials especially as the thermal interface materials (TIM) [7]. One approach to improve the thermal conductivity of epoxy resin was to introduce different kinds of inorganic fillers with high thermal conductivity [8-13]. One of the most important inorganic fillers was carbon materials, including graphene [14-19], and carbon nanotubes (CNTs) [20-23], etc., which should largely increase the thermal conductivity of the polymer-based composites due to their intrinsic extremely high thermal conductivity [5, 24]. But the ultrahigh specific surface area of micrometer-sized graphene sheets allows a large contact area with the polymer matrix. Graphene sheets tend to form irreversible agglomerates or restack on account of the strong π–π stacking and van der Waals interactions between the graphene sheets even though graphene sheets suffered from a modified process. Thus, it is hard to be dispersed in a polymer matrix with rules and orderly state. Then, it is impossible to get polymer-based composites with high thermal conductivity unless the additive amount of graphene sheets is ultrahigh. The high amount of fillers generally leads to the poor mechanical properties of the composite and improves the electrical conductivity. High electrical conductivity is normally not required in the case of TIMs.
Recently using hybrid fillers to improve the thermal properties of the composite has attracted researchers a great deal of attention. Alumina-graphene hybrid fillers help to form the effective 3D thermal conductive networks, which facilitates in reducing the Kapitza resistance and increases the transportation of phonons in the matrix.
The conductive network improves the thermal conductivity up to 8.4 W·m-1K-1 by adding 50 vol% hybrid fillers [7]. Nano-micro composite samples (either use SiO2 or Al2 O3 fillers) prepared by dispersing 1wt% nanofillers and 20 wt% micro fillers in the epoxy resin shows superior mechanical property and better thermal properties [25]. The multi-walled carbon nanotubes (MWCNTs) and boron nitride nanosheets (BNNS) provide a three-dimensional heat flow path, which makes 9 wt % of MWCNTs to be sufficient to increase the thermal conductivity of the BNNS composite from 3.12 to 4.25 W·m-1K-1 [26]. Other hybrid fillers including CNT/Bi2 Te3 [27], MWCNTs/microsized silicon carbide [28], polygonal aluminum nitride/planar boron nitride particles [29], and silicon carbide/graphene nanoplatelets [30] also improve the composite thermal conductivity greatly
Hybridization of graphene and other thermal fillers is suitable for enhancing the thermal properties of epoxy composites. Good dispersion and effective interconnection between graphene sheets are also essential for the formation of a continuous secondary phase in the epoxy matrix. Metal nanoparticles have intrinsic high thermal conductivity, so it can be applied as thermal fillers. But metal nanoparticles can’t disperse well in the matrix. If the metal nanoparticles can be decorated on the surfaces of graphene it will disperse well in the matrix and at the same time, it will act as ‘spacer’ to avoid the stack between the graphene sheets. Therefore, the high specific surface area as well as other unique properties exhibited by graphene is retained when it is dispersed into a matrix to form composites.
In this paper, the Co nanoparticles are decorated on the surfaces of graphene by using the reported method of “mix-andheat” [31]. It is a rapid, solventless, and readily scalable method to prepare various metal nanoparticle-decorated carbon nanotubes from the thermal decomposition of metal acetate/carbon nanotube solid mixtures without the use of any reducing agent. This reported method makes it possible to decorate Co nanoparticles on the surfaces of graphene nanosheet (Co-GNSs) and further prepare composites with Co-GNSs as thermal conductive fillers in mass production. Different loadings of Co nanoparticles on the GNS surfaces are studied. The scanning electronic microscopy (SEM) is applied to obtain the morphology of Co-GNSs. X-ray diffraction is also employed to characterize the obtained product. The obtained product as hybrid thermal conductive fillers is used to prepare epoxy resin composites (ERCs). The thermal conductivity (k) of epoxy resin composite samples is tested by using a thermal conductivity meter (C-THERM TCI). The lower loading of fillers can make great k enhancement of ERC indicates that the Co-GNSs are perfect hybrid thermal conductive fillers. The applications of ERCs require that the k should be weak temperature-dependent. By controlling the addition of hybrid thermal fillers and the loading of silver nanoparticles can satisfy this requirement.
Experimental
Synthesis of hybrid thermal fillers
The reported method of “mix-and-heat” is used to prepare the Co nanoparticles-decorated GNSs (Co-GNSs) hybrid thermal fillers. In the reported method, the Ag nanoparticles are successfully decorated on the surfaces of carbon nanotube, carbon nanofiber, expanded graphite, and carbon black. It also deduces that the surfaces of the mentioned carbon materials also can be decorated by other metal nanoparticles such as Au, Ni, Co, and Pd. In our previous work, Ag-GNS composites are obtained by applying the reported method. Typically, at room temperature, a certain proportion of cobalt acetate powders and GNSs with a total weight of 5g (0.5 mol % Co loading) are first mixed by using a mechanical milling method. The acetate/GNS mixture is heated in a nitrogen atmosphere above the cobalt acetate decomposition temperature (about 800℃). The cobalt acetate will convert directly into metal cobalt and form nanoparticles on the surfaces of the GNSs. The obtained Co-GNSs can be used as thermal conductive fillers directly.
Preparation of epoxy resin composites
The Co-GNSs as hybrid thermal conductive fillers is used to prepare ERCs. The direct mixing dispersion method is applied. Firstly, a certain amount of Co-GNSs is dispersed in acetone by using ultrasonic dispersion technology. Subsequently, the epoxy resin is added into the acetone dispersion with mechanical agitation and ultrasonic dispersion technology. The obtained dispersion is kept in the vaccum drying oven for being dried. The oven temperature is kept at 70o C in the vacuum condition process. The ERCs with Co-GNSs as hybrid thermal conductive fillers are obtained after being dried. By using this simple method the cost for obtaining the RECs is very low, and the composites can be produced massively. Furthermore, the most important thing is that the hybrid thermal conductive fillers can be uniformly dispersed in the epoxy resin, which can realize good micro interfacial contact between the thermal conductive fillers and epoxy resin.
Characterization
The field-emission scanning electron microscope (SEM) (S4800, Hitachi, Tokyo, Japan) is applied to characterize the morphology of Co-GNSs. The X-ray diffractometer (XRD) (D8 Advance, Bruker, Karlsruhe, Germany) is used to study the crystal structure of Co-GNSs samples. X-ray wavelength used in the analysis is 0.154 nm of CuKa. The thermal conductivities of the ERCs with Co-GNSs as hybrid thermal conductive filers are measured by a thermal conductivity analyzer (C-Therm TCi, C-Therm Technologies Ltd., Fredericton, Canada). Its test technology is based on the modified transient plane source principle. The TCi thermal conductivity analyzer includes a sensor, a power control device, and computer software. A spiral-type heating source locates at the center of the sensor, and the heat generated from the center will enter the materials through the sensor. During this process, a voltage decrease occurs rapidly at the heating source, and the voltage decrease data is used to calculate the thermal conductivity of samples. The testing capabilities of the system are 0 to 100 W/mK across a wide range of temperatures (−50°C to 200°C). The temperature of the test system is controlled by using a constant temperature box. The uncertainty of this test method resulting from the test instrument is estimated to be within ±1.0 %. In order to get more accurate data of thermal conductivity, each sample is tested for at least five times to get the average.
Result and Discussion
Morphology of Co nanoparticle-decorated GNSs
Figure 1 shows the morphology of Co-GNS samples given by SEM observation. The SEM images of Co-GNS samples with different Co loadings is separately shown in Figure 1(a), (b), (c), and (d). It is obvious that no matter the loading is higher or lower the Co nanoparticles deposit well on the surfaces of GNNs, and the sizes of the Co nanoparticles are basically uniform. The multilayer structure of GNSs is clearly shown in Figure 1(a), and the special multilayer structure supply wide surfaces for depositing Co nanoparticles. As shown in Figure 1(b) the average size of the Co nanoparticles is about 100nm, and is very uniform as the Co loading is 5 mol %. The size of Co nanoparticle increase with an increase of Co loading, such as, when the Co loading increase to 10 mol %, the average size of Co nanoparticle reaches about 150 nm, and some super big particles also form, which can be seen from the Figure 1(c). The same effect of Co loading on the average size of Co nanoparticles also can be seen from Figure 1(d) with Co loading 15 mol %. The average size of Co nanoparticles is about 350 nm. And the size of Co nanoparticles is somewhat uniform. The samples for SEM observation are prepared after the Co-GNS alcohol dispersion is centrifugated, and no Co nanoparticles deposit. It indicates that the Co nanoparticles should grow on the GNS surfaces rather than by loose attachment. Which in agree with the result given by Lin, et al. [31] identifies that using the carbon nanotube surface as the template the Ag nanoparticles grew on its surfaces.
XRD patterns of Co nanoparticle-decorated GNSs
One sample of Co-GNS nanohybrid samples with Co loading 10 mol % is investigated by XRD and the results are shown in Figure 2. Compare MDI Jade 5.0 with PDF card, the result shows signature patterns of Co metal at 36.6, 44.2, 51.5, and 76°. The 44.2 and 76°, should be corresponding to the (002) and (110) crystal planes of hexagonal close-packed (HCP) Co, and the 36.6 and 51.5 should belong to the (111) and (200) crystal planes of face-centered cubic (FCC) Co, respectively. The obtained Co nanoparticles decorated on the surfaces of GNSs is the mixture of HCP and FCC. The non-appearing of cobalt acetate diffraction patterns in the spectrum of the final nanohybrids suggests that the salt-to-metal conversion was essentially complete. The peak at 26.4°, corresponding to the (002) GNS graphitic sidewall, indicating the GNS structure is well preserved.
Thermal Conductivity of ERCs with Co-GNS as thermal fillers
The obtained Co-GNSs hybrids are used as thermal fillers to prepare Co-GNS/epoxy resin composites. The uniformity of the final composites seems to be very critical to the practical application, since it will significantly affect a series of final composite physical properties such as thermal, electrical, and mechanical behaviors. The aggregation of the thermal fillers is an important factor in decreasing the uniformity of the final composites. As the thermal fillers appear aggregation, no good thermal conductive network can form though the addition of the thermal fillers is high. Decreasing the influence of the aggregation becomes the top priority to get uniform products with high performance in mass production. Before being decorated by Co nanoparticles the GNS is firstly modified using strong acid oxidation in order to introduce polar groups such as hydroxyl, carbonyl, and carboxyl to the GNS surfaces, which can improve GNS disperse in the epoxy resin because their hydroxyl exists in the epoxy resin chains. Many reports show that higher solid content contributes to improve the thermal conductivity of the composites also decreases its mechanical behaviors greatly [32, 33]. In this study in order to get epoxy composite with high thermal conductivity and perfect mechanical behavior, the thermal filler content is confined as low as possible.
After the ERC is prepared the thermal conductivity (k) of it is also measured. Figure 3 shows the variation of thermal conductivity enhancement of ERC with different weight fraction of Co-GNS thermal fillers. The temperature is kept at 20o C. k and k0 are the thermal conductivity of ERC with Co-GNS as thermal fillers and epoxy resin, respectively. (k -k0 )/k0 is the percent of the thermal conductivity enhancement of ERC. For both kinds of epoxy composites, the thermal conductivities increase with thermal filler contents, which can be explained by the reason that the higher the solid content the easier formation of an effective thermal conductive pathway will be. Co-GNSs/ epoxy composites demonstrate higher thermal conductivities than GNSs/epoxy composites at the same thermal filler contents. When the decoration quantity of Co nanoparticles is 15mol% and the thermal filler content is 5wt% the thermal conductivity enhancement of the Co-GNS/epoxy composite reaches 327, exhibiting 2.86 times of that of the GNS/epoxy composite. This should be ascribed to the fact that the Co-GNSs as thermal fillers the Co particles link the adjacent GNSs like a bridge and also act as a spacer between GNSs to decrease the possibilities of GNS aggregation. Which avoids GNSs to form stacked graphitic structures and keep the high specific surface area as well as other unique properties exhibited by 2D graphene. An effective interconnected thermal conductive network taking advantage of the electronic heat transfer mechanism coupled with the acoustic phonons are supplied. This kind of thermal conductive network increases the thermal conductivity of the Co-GNs/epoxy composites comparing to the GNS/epoxy ones. In fact, if we take Co content into account, the real GNS content for the Go-GNS/epoxy composites is lower than that in the GNS/epoxy composites with the same thermal filler content. It also clearly indicates that the Co decoration is helpful to improve the thermal conductivity of the GNS/epoxy composite based on the above conclusion that the thermal conductivity increases with increasing GNS filler for GNS/epoxy composite.
Here, as shown in Figure 3 and Figure 4 we also need to make it clear that at any thermal filler contents and any test temperatures the more decoration of Co nanoparticles on the GNS surfaces the higher the k enhancement of Co-GNS/epoxy composite will be. This should be attributed to the size and uniform of the Co nanoparticles. As the Co decoration quantity increases from 5 mol %, 10 mol%, and to 15 mol % the average size of Co nanoparticles decorating on the GNS surfaces changes from 100 nm, 150 nm, and to 350 nm, respectively. And the size of Co nanoparticles always keeps uniform. The bigger Co nanoparticles the longer distance between the GNSs and the lower possibility of GNSs aggregation to form stacked graphitic structure will be. The other advantages of the bigger Co nanoparticles are its low interfacial thermal barrier minimizing the scattering of phonons [34, 35]. The bigger Co nanoparticles improve the synergistic effect between the Co nanoparticles and GNSs, furthermore, the different shapes from sheet to particle and different sizes from micrometers to nanometers of the GNSs and Co particles also favor the synergistic effect between GNSs and Co nanoparticles, which is good for the forming of effective thermal conductive networks [25]. The effective thermal conductive networks can facilitate phonon transfer in the epoxy resin [7,36,37]. The synergistic effect between thermal fillers with different sizes induces the formation of better percolation networks being beneficial for k enhancement [38, 39]. All of the above-mentioned factors result in the high k enhancement of epoxy resin-based composites with Co-GNS as thermal fillers. It can be concluded that the obvious enhancement of thermal properties of epoxy resin-based composites should be attributed to the high intrinsic k of GNSs, the tighter contact between Co-GNS and the resin, and the effective thermal conductive networks and better percolation networks originating from the synergistic effect between GNSs and Co nanoparticles. Our previous work shows that by using hybridization of thermal fillers silver particles and GNSs can improve the thermal conductivity of epoxy-based composites. The k enhancement can rise up to 272.9% for Ag-GNS loading at 5.0 wt% in epoxy resin as the quantity of Ag nanoparticles decorated on GNS is 1.5 mol% [40]. Goyal et al. [41] prepared hybrid graphene-metal-epoxy composites by dispersing graphene in the silver epoxy. The k of the obtained composites increases by ~500% at a graphene loading fraction of only 5 vol%. Jiang et al use graphene and ZnO as hybrid thermal fillers to prepare epoxy resin-based composites. A high thermal conductivity of 5.06W/ (mK) is achieved with 65 vol% graphene/ ZnO hybrid [42]. The unusually high thermal property is obtained, but the addition of graphene is higher compared to all our works. The more addition of graphene makes it possible to decrease the mechanical properties of epoxy resin-based composites.
The k of the ERC is also measured with changing temperatures as the temperature dependence of k is important from both physics and application points of view. Figure 4 shows the variation tendencies of k enhancement of the ERCs as a function of temperature. For all tested samples the content of thermal filler Co-GNS is fixed as 5% and the decoration quantity of Co nanoparticles is 0, 5, 10, and 15 mol%, respectively. The k enhancement shows a slight increase with temperature changing. As the decoration quantity of Co nanoparticles is 15mol% and the temperatures increases from 20 o C to 60 o C the thermal conductivity enhancement of the Co-GNS/epoxy composite changes from 327 to 442. The weak temperature dependence is beneficial for composite applications. For pure epoxy resin, due to the more intense vibration of the molecular chain to transfer heat at high temperature the k of it can increase little with an elevation of temperature. In this work, the tested temperature is not high so the effect of temperature on the k of epoxy matrix can be ignored. The weak increase of k enhancement of ERC can be absolutely attributed to the hybrid thermal filler Co-GNS. Many factors can affect the thermal conductivity of composites, and the physics of thermal transport in the investigated composites is complicated. The mechanism of thermal transport in Co-GNSs/epoxy composites includes two parts because the heat in graphene is mostly transferred by acoustic phonons while in cobalt particles it is transferred by electrons. For graphene as well as other crystalline materials stronger phonon Umklapp scattering attributes to the k decreases with increasing temperatures [43, 44]. On the other side, for the disordered and nanostructured materials, better phonon transmission trough the interfaces and decreasing Kapitza resistance at a higher temperature will result in k increase with increasing temperatures [45]. The heat transfer ability of electron in Co particles will decrease with increasing temperatures because the directional migration of electron is reduced at high temperatures. The epoxy resin is a weak conductor of heat and electrical insulator. The epoxy resin composites loading Co-GNSs as fillers will be electrically conductive. The Co-GNSs dispersing in the epoxy resin can form a 3D effective thermal conductive network and also form an electrically percolating network. This kind of epoxy resin composites can be applied in the region requiring heat transfer as well as electric conductive.
Conclusion
In summary, the thermal conductivities of the epoxy resin composites with Co-deposition on the surfaces of GNSs as thermal fillers are improved greatly. The increase of thermal conductivities of Co-GNSs/epoxy resin composites should be attributed to the Co particles linking the adjacent GNSs like a bridge and also act as a spacer between GNSs to decrease the possibilities of GNS aggregations. This kind of bridge or spacer facilitates the heat flow across the interfacial boundary, which in turn reduce the interfacial thermal resistance and improve the thermal conductivity of the composites. The number of decorated cobalt nanoparticles and temperature has a great effect on the thermal conductivity of prepared epoxy resin composites. The Co-GNSs dispersing in the epoxy resin can form 3D effective thermal conductive network and also form an electrically percolating network. This technique makes it possible for epoxy resin composites applied in the electronic package requiring heat transfer as well as electric conductive.
Acknowledgments
This work was supported by the Basic Research Foundation of Shanghai Science and Technology Committee (17ZR1410900), and the Major Project of National Science Foundation of China (51876112).
- D Yan, X Li, Y Jiang, HB Zhang, et al. (2014) Thermally conductive phenol formaldehyde composites filled with carbon fillers. Materials Letters 118: 212.
- R Sun, H Yao, HB Zhang, Y Li, YW Mai, ZZ Yu (2016) Decoration of defect-free graphene nanoplatelets with alumina for thermally conductive and electrically insulating epoxy composites. Compos Sci Technol 137: 16.
- K Zhou, R Gao, and X Qian (2017) Self-assembly of exfoliated molybdenum disulfide (MoS2) nanosheets and layered double hydroxide (LDH): Towards reducing fire hazards of epoxy. J Hazard Mater 338-343
- K Zhou, G Tang, R Gao and S Jiang, (2018) In situ growth of 0D silica nanospheres on 2D molybdenum disulfide nanosheets: Towards reducing fire hazards of epoxy resin. J Hazard Mater 344: 1078.
- ML Hao, ZX Huang, KR Saviers, GP Xiong, SL Hodson, and TS Fisher (2017) Characterization of vertically oriented carbon nanotube arrays as high-temperature thermal interface materials. Int J Heat Mass Tran 106: 1287.
- LL Ren, Q Li, JB Lu, XL Zeng, R Sun, et al. (2018) Enhanced thermal conductivity for Ag-deposited alumina sphere/epoxy resin composites through manipulating interfacial thermal resistance. Compos Part A 107: 561.
- MW Akhtar, YS Lee, DJ Yoo and JS Kim (2017) Aluminagraphene hybrid filled epoxy composite: Quantitative validation and enhanced thermal conductivity. Compos Part B 131: 184.
- YX Fu, ZX He, DC Mo and SS Lu (2014) Thermal conductivity enhancement with different fillers for epoxy resin adhesives. Appl Therm Eng 66: 493.
- W Cui, F Du, J Zhao, W Zhang, Y Yang, et al. (2011) Improving thermal conductivity while retaining high electrical resistivity of epoxy composites by incorporating silica-coated multiwalled carbon nanotubes. Carbon 49: 495.
- SH Song, KH Park, BH Kim, YW Choi, GH Jun, DJ Lee, et al. (2013) Enhanced Thermal Conductivity of Epoxy–Graphene Composites by Using Non‐Oxidized Graphene Flakes with Non‐ Covalent Functionalization Adv Mater 25: 732.
- K Ji, Y Xu, J Zhang, J Chen and Z Dai (2014) Foamed-metalreinforced composites: Tribological behavior of foamed copper filled with epoxy–matrix polymer. Mater Des 61: 109.
- SY Yang, WN Lin, YL Huang, HW Tien, JY Wang, CCM Ma, et al. (2011) Synergetic effects of graphene platelets and carbon nanotubes on the mechanical and thermal properties of epoxy composites. Carbon 49: 793.
- J Gu, C Liang, X Zhao, B Gan, H Qiu, Y Guo, et al. (2017) Highly thermally conductive flame-retardant epoxy nanocomposites with reduced ignitability and excellent electrical conductivities. Compos Sci Technol 139: 83.
- SH Song, KH Park, BH Kim, YW Choi, et al. (2013) Enhanced Thermal Conductivity of Epoxy–Graphene Composites by Using Non‐Oxidized Graphene Flakes with Non‐Covalent Functionalization. Adv Mater 25: 732.
- S Araby, LQ Zhang, HC Kuan, JB Dai, et al. (2013) A novel approach to electrically and thermally conductive elastomers using graphene. Polymer 54: 3663.
- CC Teng, CCM Ma, CH Lu, SY Yang, SH Lee, et al. (2011) Thermal conductivity and structure of non-covalent functionalized graphene/epoxy composites. Carbon 49: 5107.
- B Shen, WT Zhai, and WG Zheng (2014) Ultrathin Flexible Graphene Film: An Excellent Thermal Conducting Material with Efficient EMI Shielding. Adv Funct Mater 24: 4542.
- QQ Kong, Z Liu, JG Gao, CM Chen, Q Zhang, GM Zhou, et al. (2014) Hierarchical Graphene–Carbon Fiber Composite Paper as a Flexible Lateral Heat Spreader. Adv Funct Mater 24: 4222.
- XY Huang, CY Zhi and PK Jiang (2012) Toward Effective Synergetic Effects from Graphene Nanoplatelets and Carbon Nanotubes on Thermal Conductivity of Ultrahigh Volume Fraction Nanocarbon Epoxy Composites. J Phys Chem C 116: 23812.
- W Cui, FP Du, JC Zhao, W Zhang, YK Yang, XL Xie, YW mai (2011) Improving thermal conductivity while retaining high electrical resistivity of epoxy composites by incorporating silicacoated multi-walled carbon nanotubes. Carbon 49: 495.
- M Wang, HY Chen, W Lin, Z Li, Q. Li, M. Chen, et al. (2014) Single-Layer MoS2 Phototransistors. ACS Appl Mater Inter 6: 539
- M Bozlar, DL He, JB Bai, Y Chalopin, N Mingo and S Volz (2010) Carbon Nanotube Microarchitectures for Enhanced Thermal Conduction at Ultralow Mass Fraction in Polymer Composites. Adv Mater 22: 1654.
- HY Chen, M H Chen, JT Di, G Xu, HB Li and QW Li (2012) Architecting Three-Dimensional Networks in Carbon Nanotube Buckypapers for Thermal Interface Materials. J Phys Chem C 116: 3903.
- YW Zhu, S Murali, WW Cai, XS Li, JW Suk, JR Potts, and RS Ruoff (2010) Graphene and Graphene Oxide: Synthesis, Properties, and Applications. Adv Mater 22: 3906.
- M Liang and KL Wong (2017) Study of Mechanical and Thermal Performances of Epoxy Resin Filled with Micro Particles and Nanoparticles. Energy Procedia 110: 156.
- Kim K and Kim J (2018) Exfoliated boron nitride nanosheet/ MWCNT hybrid composite for thermal conductive material via epoxy wetting. Compos Part B 140: 9.
- H Pang, YY Piao, YQ Tan, GY Jiang, JH Wang and ZM Li (2013) Thermoelectric behaviour of segregated conductive polymer composites with hybrid fillers of carbon nanotube and bismuth telluride. Mater Lett 107:150
- T Zhou, X Wang, X Liu, D Xiong (2010) Largely Enhanced Thermal Conductivity and High Dielectric Constant of Poly(vinylidene fluoride)/Boron Nitride Composites Achieved by Adding a Few Carbon Nanotubes. Carbon 484: 1171.
- JP Hong, SW Yoon, T Hwang, JS Oh, SC Hong, Y Lee and JD Nam (2012) High thermal conductivity epoxy composites with bimodal distribution of aluminum nitride and boron nitride fillers. Thermochim Acta, 537: 70.
- B Román -Manso, Y Chevillotte, MI Osendi, M Belmonte and P Miranzo (2016) Thermal conductivity of silicon carbide composites with highly oriented graphene nanoplatelets. J Eur Ceram Soc 3987-3993.
- Y Lin, KA Watson, MJ Fallbach, S Ghose, J G Smith Jr, et al. (2009) Rapid, Solventless, Bulk Preparation of Metal Nanoparticle-Decorated Carbon Nanotubes. ACS Nano 3: 871.
- P Ajayan, L Schadler, C Giannaris and A Rubio (2000) Single‐Walled Carbon Nanotube–Polymer Composites: Strength and Weakness. Adv Mater 12: 750.
- R Rafiee (2018) Predicting mechanical properties of fuzzy fiber reinforced composites: radially grown carbon nanotubes on the carbon fiber. Compos Struct 97: 304.
- DPH Hasselman and LF Johnson (1987) Effective Thermal Conductivity of Composites with Interfacial Thermal Barrier Resistance. J Compos Mater 21: 508.
- SE Gwaily, GM Nasr, MM Badawy and HH Hassan (1995) Thermal properties of ceramic-loaded conductive butyl rubber composites. Polym Deg Stab 47: 391.
- GW Lee, JI Lee, SS Lee, M Park and J Kim (2005) Comparisons of thermal properties between inorganic filler and acidtreated multiwall nanotube/polymer composites. J Mater Sci 40:1259.
- GW Lee, M Park, J Kim, JI Lee and HG Yoon, (2006) New composites with high thermal conductivity and low dielectric constant for microelectronic packaging. Compos Part A-Appl S 37: 727.
- KMF Shahil and A A Balandin (2012) Graphene–Multilayer Graphene Nanocomposites as Highly Efficient Thermal Interface Materials. Nano Lett 12: 861.
- J Felba (2010) Thermally Conductive Nanocomposites. Nano-Bio-Electronic, Photonic and MEMS Packaging, New York: Springer, Science 978-1-4419-0040-1, 277.
- LF Chen, PF Zhao, HQ Xie, and WYu (2016) Thermal properties of epoxy resin based thermal interfacial materials by filling Ag nanoparticle-decorated graphene nanosheets. Compos Sci Technol 125: 17.
- JR Potts, DR Dreyer, CW Bielawski and RS Ruoff (2011) Graphene-based polymer nanocomposites. Polymer 52: 5.
- Y Jiang, RH Sun, HB Zhang, PMin, D Z. Yang, and ZZ Yu (2017) Graphene-coated ZnO tetrapod whiskers for thermally and electrically conductive epoxy composites. Compos Part A 94: 104.
- V Goyal and AA Balandin (2012) Thermal properties of the hybrid graphene-metal nano-micro-composites: Applications in thermal interface materials. Appl Phys Lett 100: 073113.
- DL Nika, S Ghosh, EP Pokatilov, AA Balandin (2009) Lattice thermal conductivity of graphene flakes: Comparison with bulk graphite. Appl Phys Lett 94: 203103.
- DL Nika, EP Pokatilov, AS Askerov and AA Balandin (2009) Phonon thermal conduction in graphene: Role of Umklapp and edge roughness scattering. Phys Rev B 79: 155413.
Figures at a glance