Thermal Decomposition of Bio-Insulators Manufactured with Azadiratha Indica Derivatives
Received Date:July 29, 2020 Accepted Date:August 14, 2020 Published Date:August 18, 2020
doi: 10.17303/jmsa.2020.4.201
Citation:Noel Konai (2020) Thermal Decomposition of Bio-Insulators Manufactured with Azadiratha Indica Derivatives. J Mater sci Appl 4: 1-8.
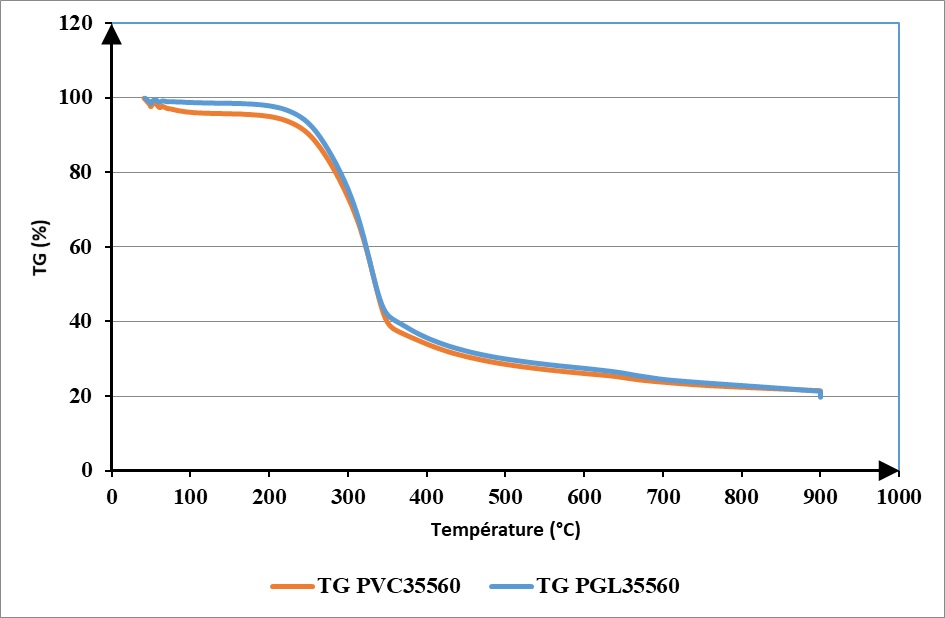
Abstract
Two thermal bio-insulators have been developed using the adhesive of Azadiracha indica tannin extract, its particles, and the exudate of Vachelia nilotica as bio-hardener. The tannin extract was characterized using the FT-MIR method. These two bio insulators PVC35560 and PGL35560 were characterized by determining their thermal conductivity, thermal strength, and their decomposition behavior. The first two thermal properties above were respectively λPVC35565 = 0.039 W/m K, RPVC35565 = 0.512 m2 K/W and λPGL35565 = 0.048 W/m K, RPGL35565 = 0.416 m2 K/W. Their decomposition modes and gaseous products emitted using pyrolysis analysis were similar. Their lower and upper temperatures limits, as well as their decomposition peaks, were different. They can be used in a building exterior structure. Their Internal Bond strength was respectively 0.6 and 0.43 MPa.
Keywords: Bio-isolators; Azadiratcha indica tannin; bio-hardener; decomposition; thermal properties Internal Bond Strength.
Introduction
Nowadays, buildings are considered as a source of energy wastage and greenhouse gas emissions. Many solutions have been proposed and taken by researchers and policy makers around the world to solve such problems. These ranged from the Kyoto Protocol held in 1997, aimed to reduce greenhouse gas emissions and the 21 st, 22 nd and 23 rd Parties Conference of United Nations Convention on Climate Change held respectively at Paris in 2015, Marrakech in 2016 and Bonn in 2017. Many countries are gradually adopting measures to improve the energy performance of buildings and reduce their dependence on fossil energies and to better insulate housing (buildings). Nowadays, buildings design includes theoretically thermal and air tightness such as heating and hot water supply equipment; air conditioning, ventilation, as well as the considerations on the compactness and building orientation, passive solar systems, and natural lighting, etc. A considerable amount of research work has been done on thermal insulation [1, 2, 3]. Some researchers have worked to control fires in buildings. This is the case for the works of Kanury et al. (1970) [4] and Roberts (1971) [5] relative to the problem of wood-burning, and the heat of reaction during the pyrolysis of wood. Other researchers have followed them working on the thermal behavior of materials made with recyclable waste [6]. Blazek (2005) [7] and Inard et al. (1997) [8] had respectively studied the kinetics reaction on the thermal degradation of polymers and developed a model capable of predicting the temperature in buildings. Other works on pyrolysis had been carried out in order to describe the thermal decomposition of the fuels studied [9, 10, 11, 12].
Considering all the above, it is of interest to manufacturing performant bio-insulators usable in buildings. It is in this perspective that the Azadiracha indica tannin and the Vachelia nilotica exudate were extracted and used in the development of particleboards usable as bio-insulators.
For this purpose, pyrolysis tests were done to study the decomposition of such particleboards bonded by Azadiracha indica tannin resins hardened, with the Vachelia nilotica exudate biohardener or glyoxal hardener and to identify the gaseous compounds emitted depending on the temperature used. Their thermal conductivity, strength, thermal, and Internal bond strength were also determined.
The Azadirachta indica and Vachelia nilotica are two trees species extensively spread across Cameroon’s Sahelian region and exploited in traditional African medicine as an anti-inflammatory, antipyretic and antimicrobial (antibacterial, antiviral, antifungal, anticandidosis...) [13, 14, 15].
Materials and Methods
Azadirachta indica tannin Extraction
In bathwater containing ground bark of Azadirachta indica, add water (bark: water ratio was 1:6), introduce a solution containing 0.4% sodium bicarbonate, and 2% sodium bisulfite. Shake continuously the mixture at 60° C for 4 hours, filter the mixture and proceed to the concentration of the liquid obtained at 60°C using a rotary evaporator. Then the liquid fraction obtained was frozen using liquid nitrogen and a laboratory spray dryer to obtain a tannin powder [16,17].
Extraction of hardeners from Vachelia nilotica trees exudates
Make an incision about 60 cm of deep on the Vachelia nilotica tree trunk using a small blade and then remove the bark manually. After fifteen days of bleeding, the exudate was collected in a container and dried at ambient temperature for three weeks. The dried exudate was finally crushed and keep in a bottle ready to use.
Adhesive development
Mix 35% tannin + 5% hardener based weight + 60% of water and adjust the pH to 10 adding sodium hydroxide. Then, stir the mixture until the viscosity reaches 600 Cp as value. The viscosity was measured using a Brookfield RV viscometer device [18,19]. Two hardeners were used: the Vachellia nilotica tree exudate and glyoxal.
Internal Bond (IB) Strength
The Internal Bond Strength of particleboards manufactured during 7 min 30 s pressing time divided into three steps (28kg/cm2 , 3min - 12kg/cm2 , 2- 5.8kg/cm2 , 2min) was determined according to the International standard NF EN 312-2 (1996) [20] using the INSTRON 4467 universal testing machine
Thermal Conductivity
The thermal conductivity of 300 × 300 × 20 mm samples of particleboard samples was measured according to ASTM C 518-85 norm [12]. The sample was clamped between two flat isothermal plates at two different temperatures. The plates were larger than the specimen and the temperature field within the sample was uniform. The formula used to determine the thermal conductivity was: λ = Φ × ∆X /∆T where: λ: Thermal conductivity, W/m K. Φ: Heat flux flowing through the sample, W/m2 . ∆X: Thickness of sample, m. ∆T: The difference in temperature between the hot and cold surfaces of the specimen, K.
Thermal strength
The thermal strength R (m2 .K / W) is function the thickness e (expressed in meter) and the thermal conductivity (λ) of the material. Its formula is given as below : R = e / λ
Pyrolysis of particle board
About 100 mg of each particle board was placed on a balance located in the furnace and heat was applied over the temperature range from 20 to 900°C at a heating rate of 10°C/min during 30 min in argon gas. This test was done using NETZSCH STA 449F3 Jupiter (Germany) equipment. The Weight gain (TG) curves and mass loss rate (DTG) were determined using excel software.
Attenuated total reflectance Fourier-Transform Middle Infrared (ATR-FT MIR)
Deposit the Azadirachta indica tannin extract on the diamond eye of the Perkin Elmer Frontier ATR-FT device. Then, screw the clamp device ensuring the contact of the sample. The tannin powder sample was scanned five times and the average of these spectra was studied between 1800 and 600 cm - 1 [22].
Results and Discussion
Extraction of hardeners from Vachelia nilotica trees exudates
This bio-hardener is mainly composed of the reactive species known as 2, 5-hydroxymethyl furan linked to carbohydrate oligomers (Ndiwe et al. 2019). These gave 2-hydroxy-5-hydroxymethyl furan and especially 2,5-dihydroxymethyl furan, these second reactive species are leading to cross-linking. (Figure 1). This bio-hardener produced from cellulose gave interesting results in the manufacture of particleboards [21].
Composite development and internal Bond strength
The Internal Bond (IB) strength of particleboards bonded with the Azadiratcha indica tannin resin and 5% Vachellia nilotica exudate biohardener was higher than that using the glyoxal as a hardener (0.6> 0.43 MPa) (figure 2). This means that the molecular weight and the rigidity (Young modulus) of the resins hardened with the exudate are higher than for the glyoxal hardened ones. These two types of particleboards can both be used for a building exterior structure.
Thermal conductivity
For particleboards measuring 190 kg / m3 density, at 2% humidity, the thermal conductivity and thermal strength values of PVC35565 and PGL35560 were respectively λPVC35565 = 0.039 W/m K, RPVC35565 = 0.512 m2 K/W and λPGL35565 = 0.048 W/m K, RPGL35565 = 0.416 m2 K/W. These two values satisfy the requirements of the French standard for particleboards (λ = 0.060 W/mK; R=0.50 m2K/W) use as thermal insulation (RT 2012).λPVC35565 and λPGL35565 are inferior to 0.060 W/mK and their thermal strength are superior to 0.50 m2 K/W. Thus, these particleboards PVC35560 and PGL35560 can both be used for temperature insulation (capable of withstanding cold and heat). The different values of thermal conductivity and thermal strength are summarized in Table 1.
Thermogravimétric Analysis
The curves in Figure 3 represent thermogravimetric (TG) analysis curves and their derivates (DTG) obtained during the pyrolysis of PVC35560 and PGL 35560 particleboards at a heating rate of 10 ° C. min-1.
These two curves highlight three main phases of mass degradation corresponding to the decomposition of a very precise volatile organic compound. The first peak of the DTG PVC35560 curve located around 50°C belongs to the first phase of mass loss [40 -150 ° C]. This peak is linked to the evaporation of H2 O and CO emitted by the resin and the wood particles. The increase of the mass-loss rate in the second phase [150 - 380 ° C] with its peak located around 334°C is attributed to the weakest chemical bonds being broken between the molecules contained in the particleboards. During this phase, cellulose and hemicellulose of the wood particles used in the manufacturing of particleboards are decomposed to form gaseous compounds such as acetic acid, isocyanic acid, and water. From 380°C to the end, another mass loss step begins. This peak located at 655°C can be attributed to the evaporation of CO, CO2 , and CH4 . This last peak expresses the total decomposition of organic volatile compounds that have already begun to degrade in the previous steps. At the end of the pyrolysis of PVC35560, there remained approximately 20.62% of the initial mass of the particleboards analyzed. This last mass corresponds to the solids segments residues of the non-consumed particleboards. The decompositions modes of PVC35560 and PGL35560 are similar (figures 3-5).
The only difference between their decomposition is at the upper and lower boundaries of the different decompositions phases and at their peak. The main gaseous compounds detected during these argon studies are summarized in Table 2.
Attenuated total reflectance Fourier transform middle infrared (ATR-FT MIR) analysis
A carefully look at the spectrum of Figure 6 permits you to identify peaks corresponding to the movements of the molecules or functional groups linked to specifics chemical structures in the range 1800 to 600 cm-1.
The small shouldering located at 764 and 818 cm-1 are associated with the C–H bending of aromatic or C–H out of plane bending of the B ring of flavonoids, C–H, or CH bending of formic acid [23]. The 1119 cm-1, 1248 cm-1, 1038 cm-1 peaks, and the 1335 cm-1 band can be attributed to the CO stretching and the deformation of C-OH and C-H of aromatics structures or others structures such as HCOOH and CH3COOH. The band located at 1594 cm-1 and the shoulder located at 1518 cm-1 are mainly occupied by the vibrations of the aromatic C = C bonds. All these functional groups C-H, C-O, C = C, and COH can be attributed to the flavonoids, CH3COOH, HCOOH, and CH4. Through these peaks, it is possible to say that there are flavonoids in this tannin extract and when this tannin extract will be degraded many gases such as CH3COOH, HCOOH and CH4 will be released.
Conclusion
The Particleboards PVC35560 and PGL35560 bonded by the Azadiratcha indica tannin resins hardened with the Vachelia nilotica biohardener are good thermal bio insulators. PVC35560 is a better thermal insulator than PGL35560. They have similar decomposition modes.
Acknowledgments
The thanks of the corresponding author are expressed to the French government for financing his research period at the LERMAB at the University of Lorraine. The LERMAB of the University of Lorraine is supported by a grant overseen by the French National Research Agency (ANR) as part of the Laboratory of Excellence (Labex) ARBRE.
Compliance with ethical standards
Conflict of interest: All authors declare that they have no conflict of interest.
- Sacadura J F (1993) Initiation aux Transferts Thermiques. Collection Tec & Doc, Lavoisier. 446.
- Brau J (1997) Théorie du Conditionnement d’Air, Institut National des Sciences Appliqués de Lyon.
- Fezzioui, Draoui B, Benyamine M and Larbi S (2008) Influence of the Dynamic Characteristics of the Building Envelope on Thermal Comfort in South Algeria. Review of Renewable Energies 1: 25-34.
- kanury AM, blackshear PL (1970) Some Considerations Pertaining to the Problem of Wood-Burning. Combustion Science and Technology 1: 339-355.
- Roberts AF (1971) The heat of reaction during the pyrolysis of wood. Combustion and Flame 17: 79-86.
- Melhyas K, Girods P, Malahimi A, Benoıt F, Yann R (2009) Thermal Degradation of Household Solid Waste in the Town of Abomey-Calavi in Benin: Kinetic Study. Waste Biomass Valor DOI 10.1007/s12649-015-9441-9.
- Blazek J (2005) Study of the reaction kinetics of the thermal degradation of the polymer. Thèse 212 de Doctorat. Institut National Polytechnique de Toulouse 262.
- Inard C, Depecker P et Roux J (1997) Un Modèle Simplifié pour la Prédiction du Champ de Température dans les Bâtiments. Revue Générale de Thermique 36: 113-123.
- Shihaden A, Hochgreb S (2002) Impact of biomass pyrolysis oil process condition on ignition delay in compression ignition engines. Energy Fuels16: 552–561.
- Aboulkas A, El Harfi K (2009) Co-pyrolysis of olive residue with poly (vinyl chloride) using thermogravimetric analysis. J. Therm. Anal. Calorim 95: 1007–1013.
- Kayagan I, Dogan OM (2008) Pyrolysis of low and high-density polyetylen. Part I: non-isothermal pyrolysis kinetics. Energy Sour 30: 385–391.
- Zhang L, Xu S, Zhao W, Liu S (2007) Co-pyrolysis of biomass and coal in a free-fall reactor. Fuel 86: 353–359.
- Govindachari TR, Suresh G, Gopala krishnan G, Banu-mathy B, Masilamani S (1998) Identification of antifungal compounds from the seed oil of Azadirachta indica. Phytoparasitica 26: 109–116.
- Sithisarn P, Supabphol R, Gritsanapan W (2005) Antioxidant activity of Siamese neem tree. Journal of Ethno pharmacology 99: 109–112.
- Ndiwe B, Pizzi A, Tibi B, Danwe R, Konai N, Amirou S (2009) African tree bark exudate extracts as biohardeners of fully biosourced thermoset tannin adhesives for wood panels. Ind Crops Prod 132: 253–268.
- Sealy-fisher V J Pizzi A (1992) Increased pine tannins extraction and wood adhesives development by phlobaphenes minimization. Holz Roh Werkst 50: 212–220.
- Navarrete P, Pizzi A, Tapin-Lingua S, Benjelloun-Mlajah B, et al. (2018) Low formaldehyde emitting biobased wood adhesives manufactured from mixtures of tannin and glyoxalated lignin. J Adhes Sci Technol. 26: 1667–1684.
- Konai N, Pizzi A, Raidandi D, Lagel M C, L’Hostis C, Saidou C, et al. (2015) tannin extract characterization and performance as an adhesive resin. Ind. Crops Prod 77: 225-231.
- Pichelin F M, Nakatani M, Pizzi A, Wieland S, Despres A, et al. (2006) Thick wood panels bonded industrially with formaldehyde-free tannin adhesives. For Prod J 56 :31–36.
- NF EN 312-2 (1996) Particle board requirements: requirements for panels for general use used in dry environment.
- Ndiwe B, Pizzi A, Tibi B, Danwe R, Konai N, Amirou S (2019) African tree bark exudate extracts as biohardeners of fully biosourced thermoset tannin adhesives for wood panels. Ind Crops Prod 132: 253-268.
- Konai N, Pizzi A, Raidandi D, Lagel M C, L’Hostis C, Saidou A, Hamido S, et al. (2015) Aningre (Aningeria spp) tannin extract characterization and performance as an adhesive resin, Industrial Crops and Products 77 : 225-231.
- Socrates G (2000) Infrared and Raman characteristic group frequencies: tables and charts/George Socrates, 3rd edn. Wiley, Chichester, New York 45–53.
Figures at a glance